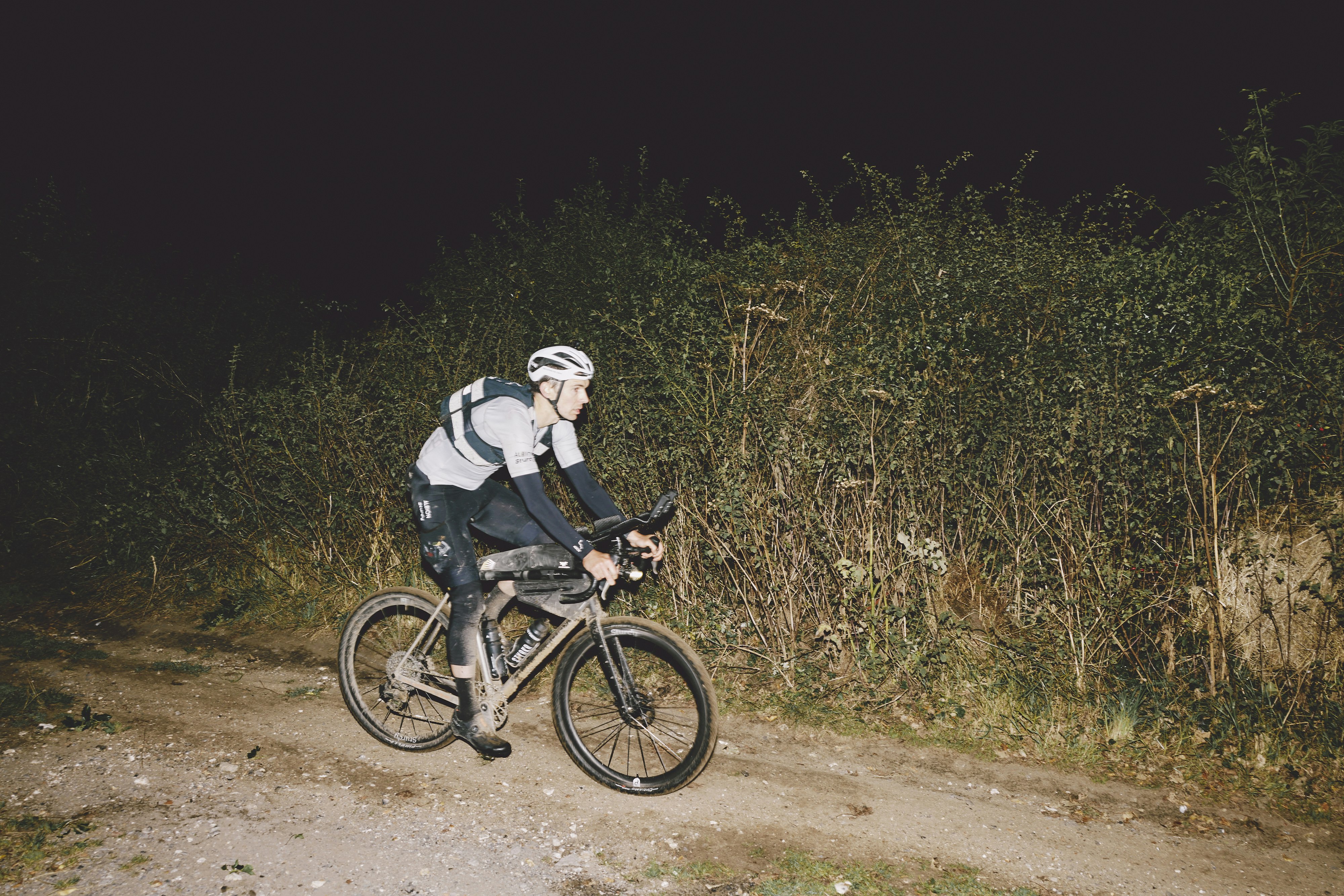
Albion X Sturdy Cycles
10 15 24Words by Charlie Stewart, photos by Harvey Waller.
If you could create the perfect bike and clothing system for an ultra race, what would you do?
This was a question that Tom Sturdy and I thought might be an interesting one to try and answer, as a way for our two brands to collaborate.
I had admired the Sturdy brand from afar for a little while. The combination of their raw, almost brutal aesthetic that was also highly considered and beautiful made the bikes incredibly intriguing and distinct.
Conceptually, titanium seemed like the right material to make a bike for long distance racing out of, especially one with a mixture of road and off road surfaces, and Sturdy has integrated this material into their designs in a more complete way than anyone else out there.
Trying to create the perfect products for long distance riding is something that we think about all the time at Albion, so the opportunity to dial in on a specific race and test some ideas was an exciting one for the team.
We picked Further East as the race, a 685km, 50/50 road/off-road time trial around East Anglia.
The event presented an enticing mixture of distance and terrain that would put the thinking and products of both brands through their paces.
THE BIKE
Sturdy offers a custom service, whereby the brand has a few distinct models that have been developed for various disciplines that are used as the starting point for the customer to have a made to measure bike created for them.
The Cilla is Sturdy’s gravel bike, so this was the starting point for the machine that would take on Further.
Taking my measurements, we then created a geometry and spec for the build.
Further East is a very flat course, and with half of the 685km route being on the road, the ability to be fast on these sections needed to be balanced with a set up that could handle some very rough, rutted bridleways. An interesting challenge when deciding what set up to run.
When the bike was ready, I headed down to the Sturdy workshop in Frome, Somerset to collect it, and had the chance to talk to Tom Sturdy about his approach to designing bikes.
Tell us about how you got started with making bikes? Why does Sturdy exist?
I initially started messing around with making bikes to better understand how you could change the performance of a bike by altering either the geometry or the structure of it. When I was racing I was lucky enough to have the use of a really nice range of bikes that were great on paper, but it always puzzled me how some were so much better than others. My academic background is in a mixture of Aerospace engineering and sports biomechanics, focusing on bikes was a great opportunity for me to combine those fields.
What I love most about manufacturing bikes is that I'm able to be involved and develop expertise in every aspect of the lifecycle of the product from initial brief right through concept design, engineering, fabrication all the way to finishing and assembly. It's a pretty rare combination in modern engineering and manufacturing, on the face of it they are a wonderfully simple product but the reality is that there is no end of complexity to dive into.
Your background is in racing, you were a professional triathlete, how has that informed what you are doing with Sturdy?
It's been a really important part of developing the products that leave the workshop today. I don't race triathlons anymore but still enjoy riding at a respectable level across a range of disciplines and plan on doing so for as long as I care to ride bikes. I don't ride as many miles as some of my customers but over the years I've built up a pretty accurate sense of how I want a bike to perform. It's not that the bikes I make are only for people who race, far from it, more that my experience of pushing myself and equipment has been a really valuable resource when developing and evaluating designs.
Your bikes have a very distinct aesthetic, what is your view on how performance and aesthetics should combine?
Everything I do is definitely function led but I believe that if this is done well then form follows hand in hand. I'm a big believer that a design is finished when there's nothing left to take away rather than nothing more to add.
There's a huge amount going on in the design of the bikes that I make that is hidden in plain sight. It's important to me that the bikes are a pleasure to build as well as to ride. I spend a decent amount of my life building them after all! A big part of the challenge is designing for one part of the process in a way that doesn't detract from another aspect of the product.
You use titanium to make your bikes, why is this your preferred material?
It's a really versatile material that affords me good design versatility. In terms of its mechanical properties it sits nicely in the middle of those commonly used to build bikes; it is stiffer than carbon and aluminium, not as stiff or as heavy as steel. I use additive manufacturing extensively and titanium lends itself very well to his process too. Its resistance to corrosion lends itself well to the general design ethos behind the bikes and ensures that the bikes are the 'lifetime' bikes that I want them to be.
You are unique in that you machine more parts than a lot of other bike makers, including chainrings, jockey wheels and brake levers among other things. Why did you decide to go down this route and how do you think this affects the performance and feel of the bike?
When I first started building frames in a much more traditional way I was always a bit frustrated that whilst, on the surface I had what appeared to be lots of choice (in terms of what tubing I could use and what bottom brackets, head tubes, dropouts etc that I could attach them to), in reality I was just fabricating from the same 'bill of materials' and in the same way that many other manufacturers were and then assembling the bikes with the same components. I felt that having more input over the structure of the frame itself was an important way to have a greater influence over the end result. As I started refining designs on that level it quickly became apparent that the bike as a whole is a relatively complex system and so there was a benefit in being able to fully understand and ultimately control how all of the parts interact.
Some of the parts we make are much more of a 'bi-product' than others but I think even these small relatively peripheral touches come together to make the bike as a whole a really nicely considered piece.
Can you talk a bit about the process of how you create a bike for a customer? What could someone expect if they decided to purchase a Sturdy bike?
Once a customer is happy to commission a build we will work with them to work out a detailed brief, establish bike fit information and ultimately agree on a geometry design and a detailed specification. We offer 'models' of bikes that set down broad spec ranges or benchmarks that form useful starting points in this process. As we design, build, finish, ride and maintain the bikes on a daily basis we also have go-to recommendations at all points of the process for what we know works well but ultimately it's a collaboration between us and the customer.
When a geometry and specification is agreed I'll convert the geometry design to an engineering design from which the build will be manufactured. As the fabrication gets underway we'll also fix the finishing plans for the aesthetic of the bike. Again we have recommendations as to what can work well and what lasts the test of time but it's always a collaboration to make sure each customer gets the aesthetic that they are looking for.
Tell us a bit about how you approached the bike for Further East?
In many ways the approach was no different to any other of the builds that we do. The exception to that being that the brief was much more specific than we would typically get, especially for a gravel bike.
The long distance nature of the event meant that there was an inherent level of versatility needed but things like tyre sizes, gearing, loading of the bike were all very much known. The requirement to cover ground fast, but for an extended period of time, also meant that a lot more was known about the rider position. All in all it meant that certain aspects of the geometry could be fine tuned for a specific type of riding (and notably riding when the rider is extremely fatigued).
This doesn't mean, of course, that the bike can't be used for other events but it's not often that I get to consider what would be best suited to one very specific application.
What does the future of Sturdy Cycles look like? I know you have recently announced that some 'off the shelf' bikes will be available?
The addition of some 'off our peg' bikes is quite a big change for us and it will be interesting to see how that ends up sitting in terms of overall workload. They aren't intended to replace what we currently do but I wanted to give customers who don't want or need something made to measure the option of a UK made frame that they don't have to wait too long for.
The bikes we make are always evolving (it's a key benefit of using additive manufacturing) and I am nearing the end of a big round of development that will be rolling out across all the models that we currently offer which will be an exciting one to reveal. The last few years have seen really big changes here in terms of both the workshop and production so I am actually looking forward to slowing the rate of change down a little bit!
The full spec of the bike was as follows:
Frame - 3D printed Ti construction with fully internal cable routing and custom geometry
Fork - 3D printed Ti with internal cable routing
Seatpost and seat clamp - 3D printed Ti seatpost topper - integrated seatpost clamp
Cockpit - 3D printed Ti with fully internal cable routing and custom geometry
Crankset - 3D printed Ti in custom length
Chainring - Custom machined Ti X1 chainring (46t)
Groupset: SRAM Force etap 1x (custom Sturdy ti brake levers and jockey wheels)
Computer and accessory mount - 3D printed fully adjustable mount with head unit mount and lower accessory mount.
Bottom bracket - Custom machined Ti T47 bottom bracket with Enduro bearings and Sturdy BB tool
Through axles - Custom machined Ti through axles
Bolts - Custom machined Ti Torx head bolts with included tool
Bar end plugs - Custom machined Ti bar end plugs
Rotor lockrings - 3D printed Ti - same installation tool as BB
Wheels: Sturdy Carbon Spoke Wheelset
Tyres: Pirelli Cinturato Gravel RC
Aero bars: Wattshop Minimoi
Lights: front: Exposure Race, back: Exposure Blaze
Head unit: Coros Dura
THE CLOTHING
When thinking about the clothing and equipment for a race like Further East, for me there were three key considerations: comfort, aerodynamics, and weight.
The balance of comfort and aerodynamics in clothing for an event like this was going to be important to get right. The speeds and the mixture of terrain mean that whilst on some parts of the course aero was going to be important, on others, it wouldn’t really matter at all and comfort would be much more beneficial.
Add in the fact that it was (in the end) a 33 hour continuous ride with less than 30 mins stopped time including through the night, and the potential variables in terms of weather and light conditions, and you can start to see how having a very dialed clothing set up was going to be a big advantage.
For my base layer I opted for an Albion short sleeve merino layer, which I find to be by far the most versatile in terms of comfort and temperature management in all but either very hot or very cold conditions. The temperature range for the race was quite varied, starting in the low single digits celsius and getting up to the high teens and down again through the day, night and the following day.
We created a custom ‘ultra speed suit’ using the Albion Lightweight Short Sleeve Jersey and ABR1 Pocket Bib Shorts as the basis, combining them to reduce weight and bulk and improve aerodynamics. This prototype idea was also used by Justinas Levieka to win The Tour Divide in a new record time this year, and the concept of an aero suit for this type of racing is an interesting one that we are gathering information and feedback on.
Another prototype product in use on this race was a new active fleece gilet using Primaloft Active Evolve that will be added to the Albion range early next year. This is a really fantastic product that I am very excited about, so simple in many ways but the fabric really is something special in terms of its ability to regulate your body temperature in accordance with your level or exertion, and also provide insulation when covered by a windproof layer.
I carried two jackets, the Albion Ultralight Insulated Jacket and a lightweight prototype Pertex Shield 2.5 layer rain jacket.
The Ultralight Insulated Jacket has become a staple of riders kit lists for these events for its extreme packability and warmth to weight, and it was the obvious choice as my warm layer for when needed. Weighing under 100 grams for a size medium, you barely notice you are carrying it and it is exactly the right layer for riders looking to minimize weight but also have access to a warm, windproof layer.
There was no rain in the forecast so I carried a rain jacket really as an additional windproof layer that could be used in the rain if the forecast wasn’t accurate. I find Pertex Shield fabrics to be really effective and comfortable windproof layers, as well as wet weather protection.
The Albion Visibility Cargo Vest was used to carry additional layers, spares, food etc. Super comfortable and lightweight, and with the added peace of mind of 360 degree reflectivity when riding on the road and at night.
THE RACE
In short, everything came together and I was able to get back to the finish in 1st place, in a total time of 33 hours, two minutes and five seconds.
My equipment was flawless, and it was very rewarding to be able to conclude the project with winning the event and to provide an answer to the question that brought Albion and Sturdy together to experiment in this way.
For some more detail on the race itself, I answered a few brief questions for Dotwatcher that you can find here.
A big thank you to Tom Sturdy in particular, but also Jack and Omar at Sturdy Cycles for bringing the bike to life.